Quest for the Optimal Pipe SizeYou want to pump 600 gpm of liquid from point A to point B. What is the correct pipe size for your new system? The simple answer is it depends on what you are pumping, how fast you want the process to occur, how far you are pumping and the duty cycle. The other key question is how much money do you have? Many people will select a pump, look at the discharge size and assume the pipe size should be the same as the pump. This course of action is typically an expensive mistake because the pipe size will be too small. Initially it appears to make sense because the optimum pipe size would be the smallest diameter size simply based on the cost of the pipe per foot. However, if you are pumping sulphuric acid or suspended solids (slurries) the resultant high velocity would quickly erode the pipe. The system would have a short, unreliable, and costly life. The key factor to consider is what it will cost to pump the liquid over some period of time. The smaller the pipe size, the more energy it will cost to pump the liquid due to the higher friction losses. The larger the pipe size, the lower the friction factor and the corresponding cost to pump the liquid. Of course, the larger pipe size carries a higher initial cost for the project. There will be a just right “Goldilocks” choice of not too big or not too small.
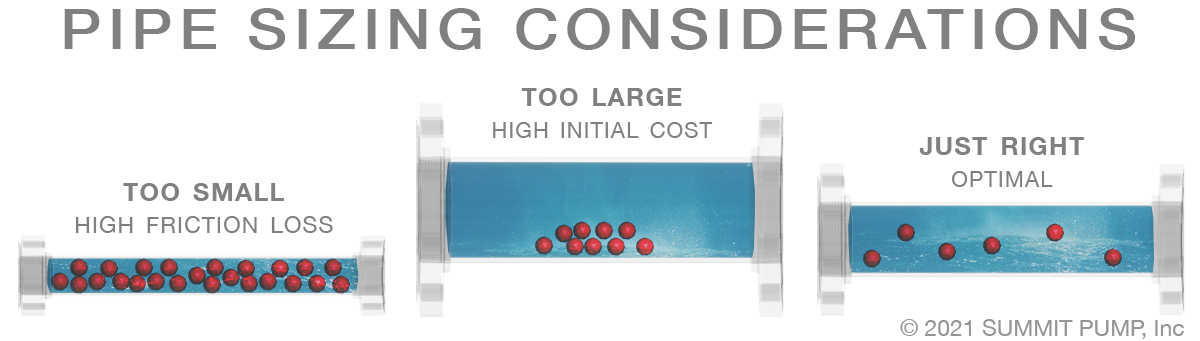
We can’t drill down into the selection details in this forum, but if you need assistance, the US Government Department of Energy (DOE) will be a good source of information. Also see my February 2021 “Pumps and Systems” article on this subject. What's the Value?For today’s exercise let’s assume we are pumping ambient temperature water with little to no suspended solids. Let’s also assume the difference in static head (liquid elevation) between the two points is fairly small. From an energy efficiency aspect, we can’t do much about the difference in static head in any system, but we can address the other main factor which is friction.
We typically suggest flow velocities to be around a nominal 10 feet per second on the discharge side of the pump. For a 6-inch pipe that would result in a flowrate of 850 gpm and for and 8-inch pipe it would be 1500 gpm.
Given a 70% efficient pump that is operated 8700 hours per year at an electrical cost of 5 cents per kilowatt hour. The DOE estimates that to pump 600 gpm a distance of 1000 feet would cost $1,690/year for a 6-inch pipe …and $425/year for an 8-inch pipe. Even for this simple example you can see the marked difference in cost by changing one pipe size. Pay Me Now or Pay Me Later For your system, look at the cost of the pipe based on size and compare to the energy cost to pump the liquid over time. Plot these two costs on a graph/chart. Normally these are exponential functions, so it will be a curve. Once plotted you will see the optimum pipe size versus the energy costs over the design life of the system will be where the two curves cross. You can have an initially cheap installation that will cost you in energy and maintenance over time… or you can pay a few more dollars up front for larger pipe and reap the benefits of a reliable and energy efficient system for many years. 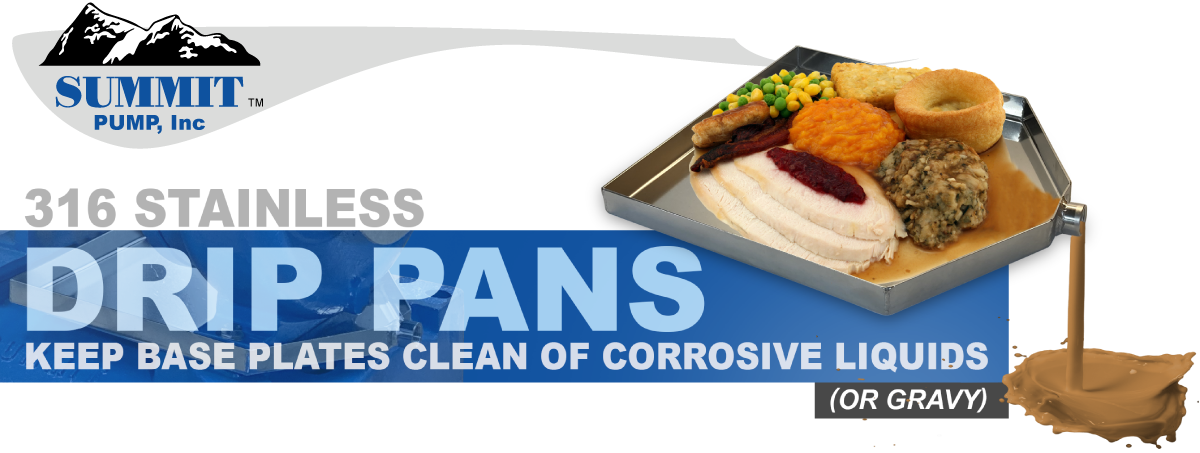 |