In high school, I received a water-resistant watch for my birthday. During the same time, I was also taking SCUBA lessons at the local YMCA. I soon discovered that water resistant does not mean waterproof. Fast forward 55 years and I witness pump owners applying standard pumps into harsh slurry services and expecting great results. These owner-operators are then both surprised and disappointed when the pump fails prematurely, because the pump was perhaps wear resistant but it was not wear proof.
Know Your Slurry: In essence there are four classes of slurries covered in Hydraulic Institute/ANSI Standard 12.1-12.6 (2016). The ANSI standard explains how the classes are progressively defined by solid size, shape, type, population, and specific gravity. The determination and ranking of the slurry class is the important first step to help you pick the proper pump, speed, and materials of construction for the service. Slurries that are corrosive and viscous, especially when coupled with higher temperatures will add another factor in the decision process. Normally for a slurry application, beside the flowrate and total head, we also need to know the following information about the liquid / slurry properties: 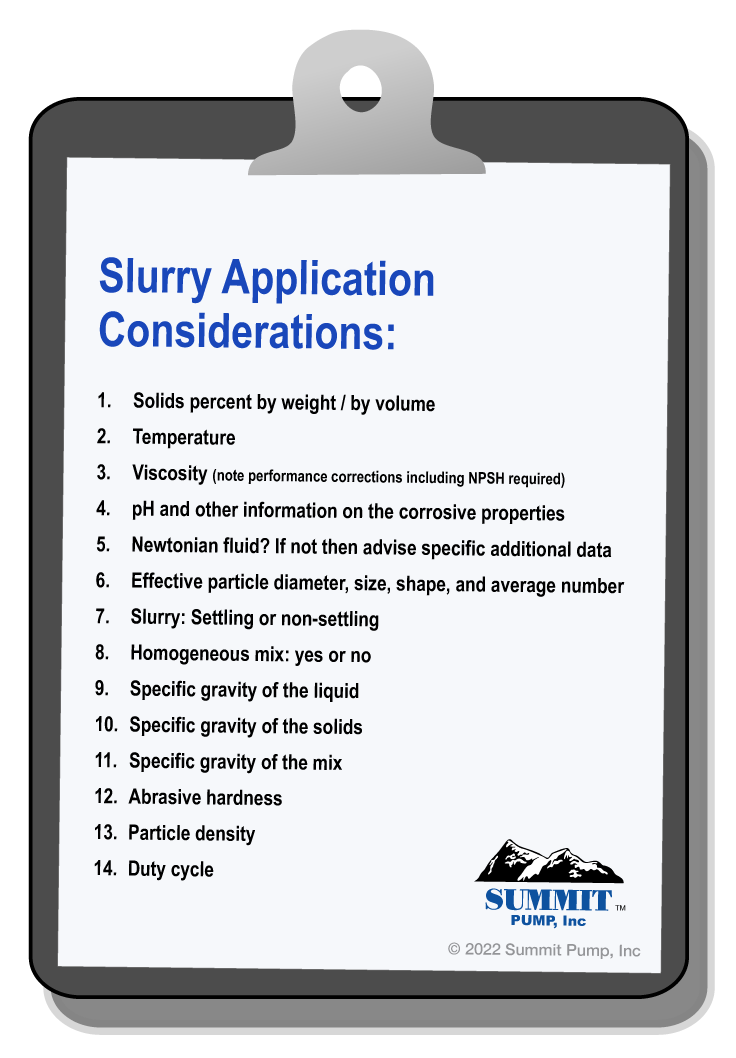 Slow Your Roll:Pump wear is directly related to the pump speed and duty cycle. The commonly accepted and best practice thumb rule is that pump wear is proportional to the pump speed cubed. We will always advise to keep the speed as low as possible. The mantra of engineers for slurry applications are pumps that are “big and slow”. We recommend that it is often better to have two (or more) properly spaced lower speed pumps in series than to let one pump generate all of the required head. Impeller tip speed is another important factor and often misunderstood. You may look at an application and prefer the faster 12-inch impeller that can do the same hydraulics as a slower 24-inch impeller. The impeller tip speeds may be the same for each pump, but over time industry studies have shown that pump wear is more closely related to the actual pump speed (rpm) than it is to the impeller tip speed. 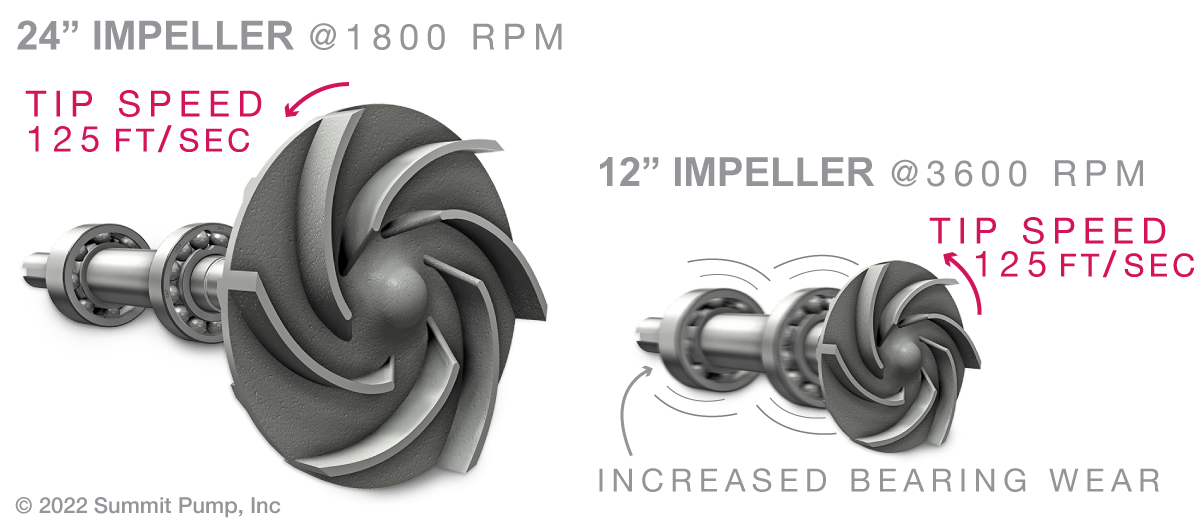 It is still important to consider the peripheral speed and the recommendations for the maximum impeller tip speed are as follows: Maintain a Healthy Pump Life: It is imperative to operate the pump as close to the best efficiency point as possible to avoid recirculation wear issues. Slurry recirculation is, in essence, “an effective and efficient sand blasting method for pump internals”. 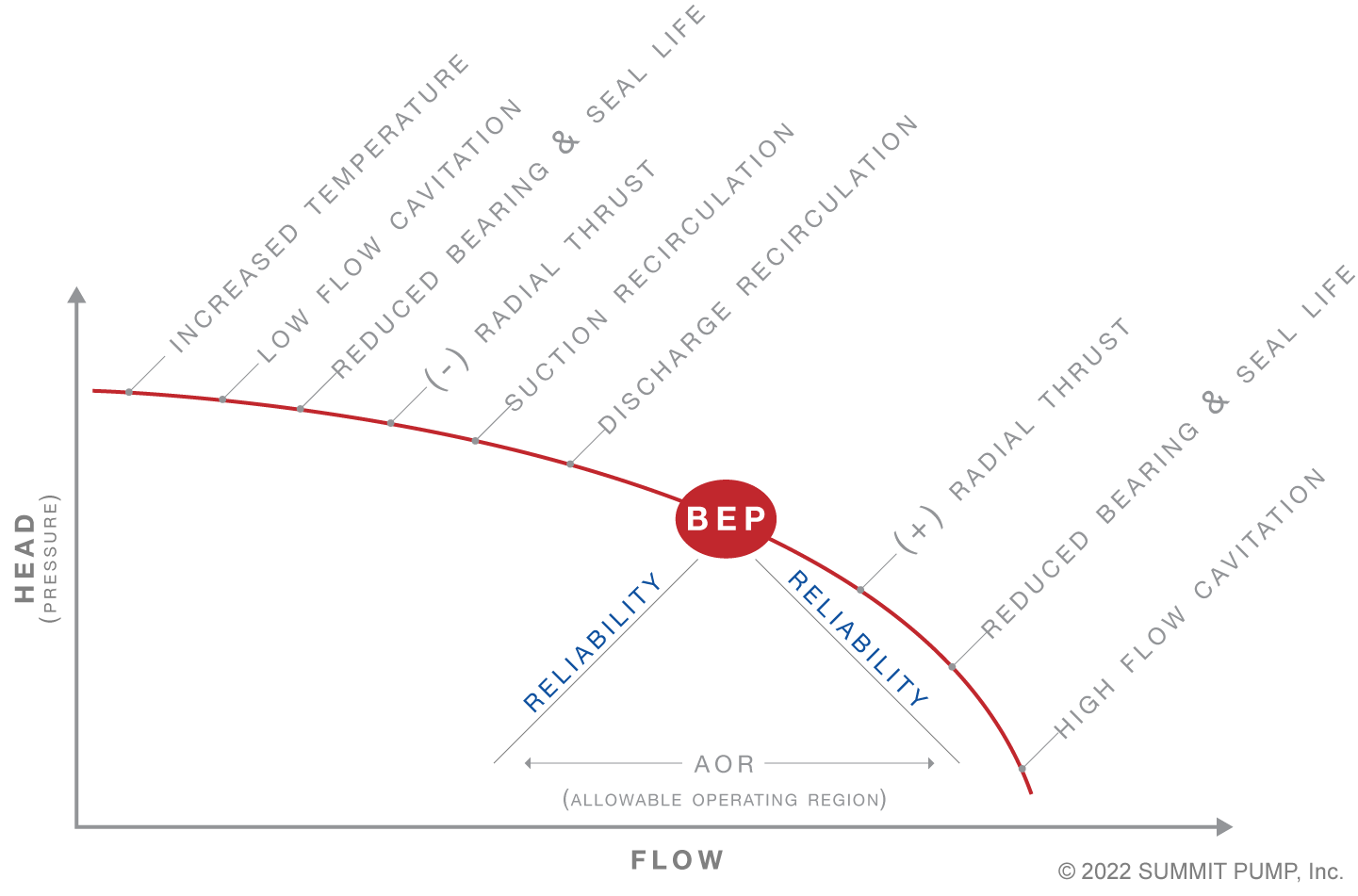 Slurry pump impellers wear faster than those in other services; It is important to have them balanced both initially and often. There are many good reasons why slurry pumps have beefy bearings and unbalanced impellers is one of them. Application data sheets are available on our webpage to assist in selection. Don’t let your next slurry pump application be a failure. Put the right pump in service. 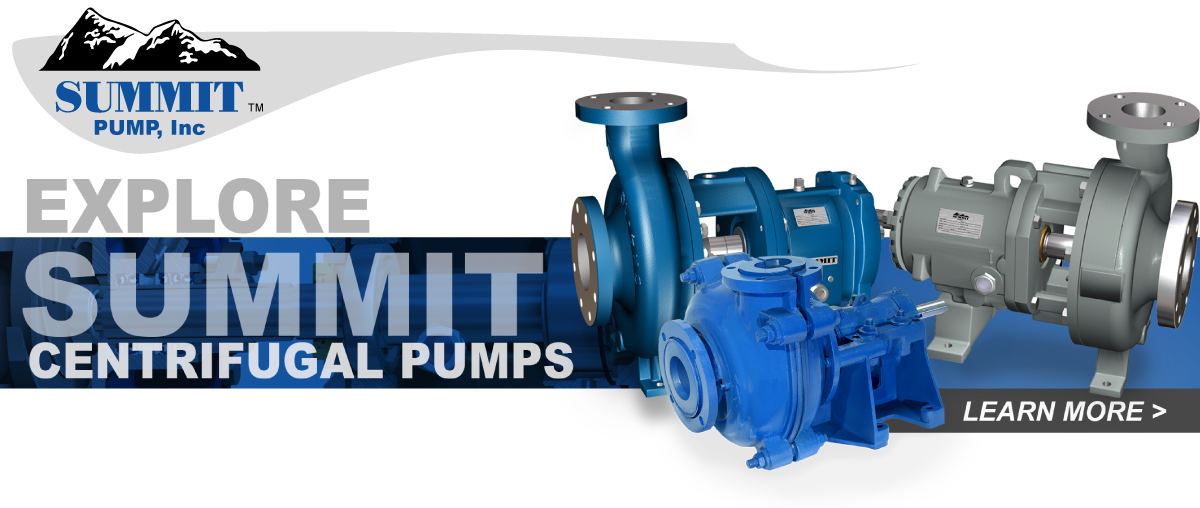 |