Reduced shaft deflection results in greater shaft, bearing and mechanical seal longevity. This directly translates to increased reliability with a subsequent decrease in vibration and noise. All these factors will reduce pump total cost of ownership (TCO).
Background When we first set course on the journey for reliable pump selection it is always prudent to thoroughly review how the pump will
actually be operated and the liquid properties. I point this out because pumps are rarely operated at the desired/design coordinates. We all aspire for the pump to operate at the best efficiency point (BEP) or at least in the preferred (heart) of the allowable operating region (AOR), but real-world obstacles will frequently preclude us from reaching the goal. Besides the pump operating point on the curve, shaft deflection is a function of many factors that include speed, shaft diameter, cantilevered length, and the geometry of the impeller. When coupled with additional negative factors like unbalanced impellers and bent shafts, deflection will be even worse.
Determining Deflection In lieu of explaining the calculation of radial forces, determination of minimum flow and/or the Youngs Modulus of shaft materials; this month I simply want to remind our readers to consider a few general tips regarding shaft selection. Most pump people are aware of the pump grading tool known as the
“L over D” ratio (L
3/D
4). This tool is also known as the (shaft) slenderness ratio, deflection ratio or stiffness ratio. “L over D” is an index of shaft robustness and because it is a ratio there are no units. The ratio is a counterintuitive coefficient that describes the shaft’s ability to resist deflection due to the varying radial hydraulic forces during operation. The lower the number the better the shaft is able resist deflection. The lower ratio predicts a longer life for the mechanical seals, bearings, wear surfaces and overall increased pump reliability.
Note: “L over D” ratio is only relevant to single stage, overhung, end suction pumps. For example ANSI pumps (B73.1-2020) and other rotodynamic pumps with geometries designated as “OH” (refer to Hydraulic Institute).
Shaft Selection Ideally you would select a solid shaft over a sleeved shaft. With today’s technical advancements in cartridge mechanical seals most applications can be handled successfully with solid shafts. The increase in shaft diameter will pay for itself in less downtime.
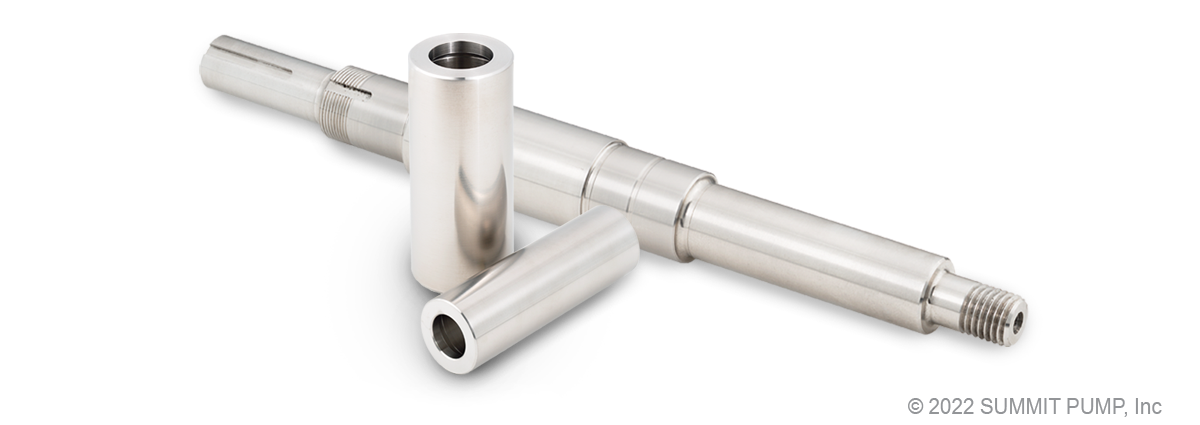
For a given pump/system issue you can’t always treat the root problem, but you can frequently address the symptoms and in some cases,
you have viable choices. For example, mid-size ANSI pumps (Designations A-05 through A80) have the option to utilize an oversize shaft (LT versus an MT frame and shaft); The reduction in “L over D” ratio is significant.
Decision Factors:
It is more important to select a larger diameter shaft (lower ratio) when...
- The pump will be operated closer to minimum continuous stable flow (MCSF) than BEP
- The Suction Specific Speed (Nss) is higher (as Nss approaches 11,000 the allowable operating region reduces to a narrower envelope)
- The speed, flow, and head are high (a heftier shaft is exponentially more important on a 200 bhp pump than on a 5 bhp application)
- The impeller diameter is closer to maximum (radial force is a direct function of the impeller diameter)
- The impeller b2 dimension is wider (radial force is a direct function of the width)
- The specific gravity (SG) is higher (radial force is a direct function of the SG)
- The viscosity is higher
- The duty cycle is continuous versus intermittent
- The impeller (rotor) balance is out of specification
- The casing is a single volute design in the larger sizes (The robust shaft requirement is reduced when the pump casing design is either a diffusor or dual volute)
- The casing is a standard nonconcentric (impeller center offset from casing center) design. If the pump is of a concentric design like a low flow-high head or a recessed impeller pump the need for a robust shaft is reduced.
Notes of Caution:- Do not overlook shaft material compatibility with the liquid
- It is understood that pumps utilizing packing will require a sleeve, but deflection is less due to the “Lomakin effect” of the packing
When in doubt check with your RSM or engineering for further guidance. I have also written several technical columns on the subject, please see the links below:
Solid Shaft Designs and Cartridge Seals Why Does My Pump Shaft Keep Breaking
Minimum Flow Redux Casing vs. Impeller
What is the Root Cause of Shaft Failure