Even the Best-Laid Plans Sometimes go Wrong...
The long road to reliable pump life is often paved with good intentions…but sometimes there are unintended consequences. When system designers place strainers on the suction side of a pump it is ostensibly to protect it, and yet in reality it will be the strainer that kills the pump.
Most centrifugal pumps are designed to handle some amount and size of solids. The manufacturer will advise what solids the pump can handle. When trying to protect system components other than the pump it is a better idea to place the strainer on the discharge side of the pump.
What’s the Problem? The are several issues with placing the strainer in the suction line. Simply stated, it can prevent the suction system from properly delivering liquid flow to the pump. The main problem is that the strainer will inevitably clog and force the pump to run dry.
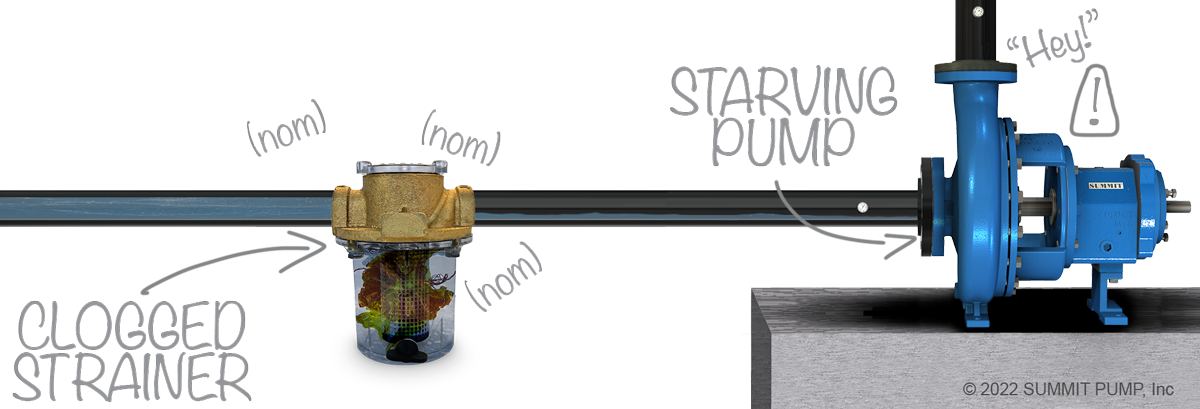
The second issue is that before the strainer fully clogs there is a marked reduction in net positive suction head available (NPSH
A) causing cavitation. There are also issues with the increase in turbulent flow, because impellers work better if the flow is laminar.
You Must Have Strainers on the Suction Side… Now What?
Calculate: Strainers are engineered and selected to keep the pressure drop across them down to an acceptable and safe level. Each strainer will have a resistance coefficient (CV) assigned by the manufacturer. A simple definition of CV is that it is equal to the number of gallons per minute that can flow through the strainer with less than or equal to a 1psi drop.
Implement: The best action is to add instrumentation and monitor the differential pressure (DP) across the strainer. I suggest it is better to use a duplex gauge than to use two separate gauges due to differences in system losses and gauge inaccuracies. A differential pressure transducer is normally better than a duplex gauge.
In the field the DP across the strainer for both clean and dirty conditions should be determined by empirical means. You can compare the low value of DP (clean strainer) to a higher value (clogged strainer) as a benchmark range indicator for required action.
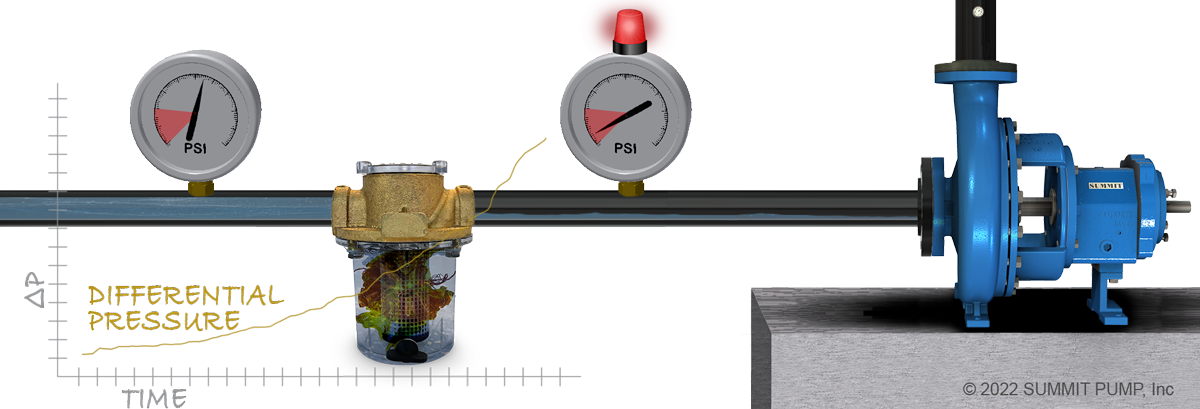
If the DP across the strainer is not automatically monitored and alarmed then an operator must check on a regularly scheduled basis. Readings should be recorded to watch for protracted trends and immediate action taken if the DP is out of specification. Even 1 or 2 pounds per square inch (psi) can be the difference between success and failure.
Bottom Line From the perspective of industry best practices, I suggest thinking long and hard before placing a strainer on the suction side of the pump.